Understanding Precision Mold Parts: The Backbone of Precision Engineering
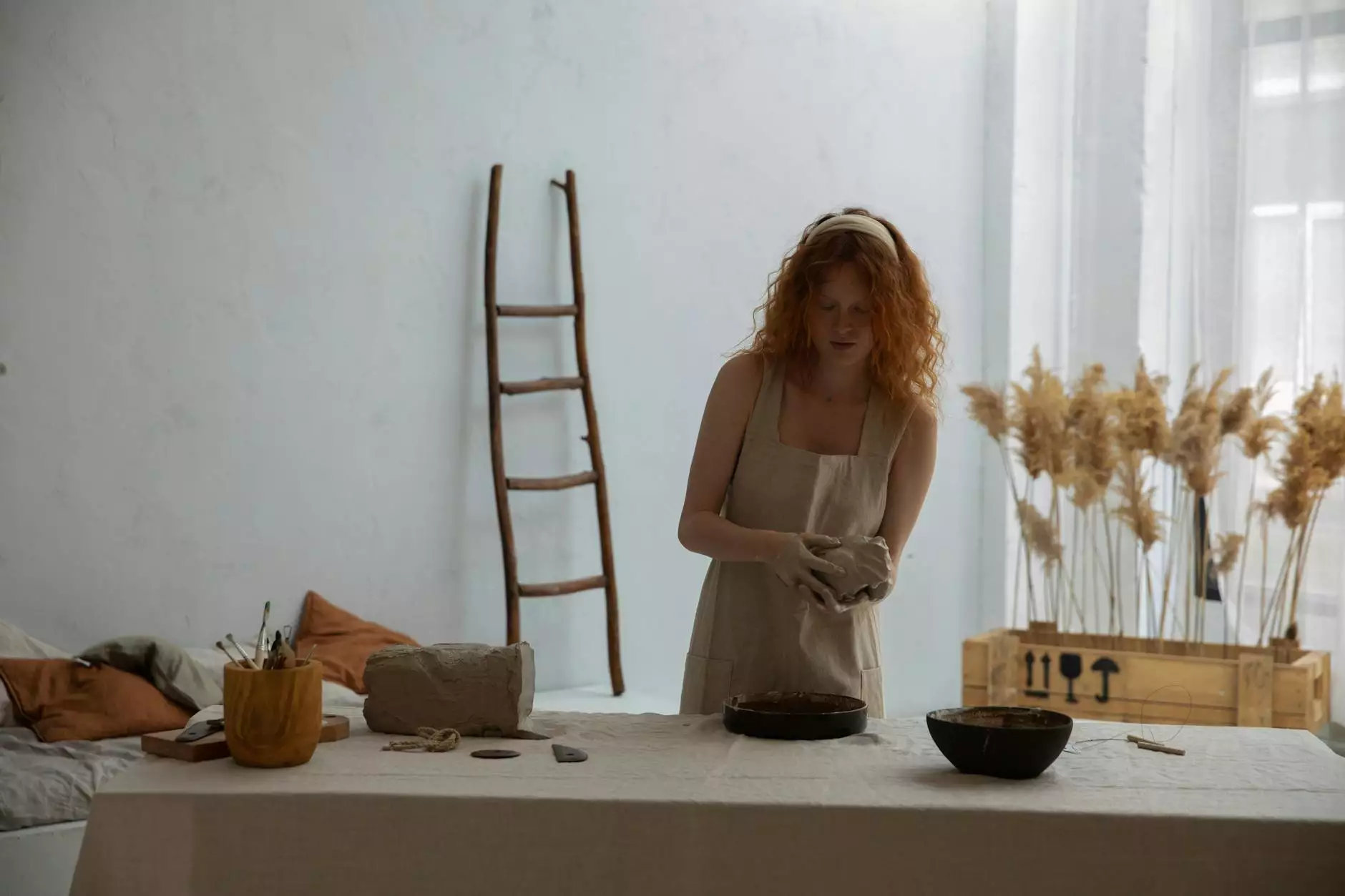
In today's highly competitive manufacturing landscape, the demand for precision mold parts continues to grow exponentially. Industries ranging from automotive to electronics rely heavily on these components to ensure the high quality and efficiency of their production processes. This article explores the intricacies of precision mold parts, their applications, benefits, and how businesses can leverage them to enhance performance and productivity.
What are Precision Mold Parts?
Precision mold parts are specialized components used in the manufacturing of molds, which are essential for shaping various materials like metal, plastic, and composites. These parts are engineered with the utmost accuracy to achieve the desired form, fit, and function of the final product. The manufacturing of these parts typically involves advanced technology, including CNC machining, electrical discharge machining (EDM), and additive manufacturing techniques.
The Role of Precision Mold Parts in Metal Fabrication
In metal fabrication, the role of precision mold parts is pivotal. They are instrumental in achieving tight tolerances and high levels of repeatability, which are critical for producing components that meet industry standards. Here are some key areas where precision mold parts play a crucial role:
- Consistency: Precision mold parts ensure that each produced piece meets the exact specifications, providing uniformity across large batches.
- Quality Control: With precision, manufacturers can execute rigorous quality checks, reducing defects and waste.
- Efficiency: High-quality molds reduce production time and costs, allowing businesses to operate more efficiently.
Why Precision Matters
In manufacturing, the phrase "cut once, measure twice" resonates deeply, especially when it comes to the fabrication of precision mold parts. Here’s why precision is crucial:
1. Cost-Effectiveness
Investing in precision mold parts may seem high upfront, but the long-term savings are significant. Precise molds minimize the likelihood of errors during production, leading to:
- Reduced material waste
- Lower labor costs due to fewer reworks
- Enhanced overall productivity
2. Enhanced Product Lifespan
Accuracy in mold design directly impacts the lifespan of the finished products. Carefully crafted molds can withstand repeated use without compromising the integrity and detail of the components produced. This reliability fosters trust between manufacturers and their clients.
3. Regulatory Compliance
Many industries are governed by strict regulations that demand high-quality standards for manufactured parts. Utilizing precision mold parts helps businesses adhere to these standards, ensuring their products are compliant and safe for the market.
Applications of Precision Mold Parts
Precision mold parts find their application in various industries, each benefiting from their unique characteristics:
1. Automotive Industry
In the automotive sector, precision is everything. From engine components to body panels, every part must fit perfectly. This industry demands molds that can replicate intricate designs while maintaining durability. Some applications in this field include:
- Engine components
- Body parts
- Interior fittings
2. Medical Devices
The medical sector requires molds that can produce components with extreme precision, essential for devices such as surgical instruments, prosthetics, and diagnostic tools. Any deviation can lead to severe consequences, which is why investing in high-quality precision mold parts is non-negotiable.
3. Consumer Electronics
Consumer electronics feature complex designs with small tolerances. Perfectly crafted molds reduce gaps and enhance the aesthetic appeal of products, which is vital in this competitive market. Applications include:
- Smartphones
- Tablets
- Wearable technology
Challenges in Manufacturing Precision Mold Parts
While the advantages of precision mold parts are clear, manufacturers face several challenges in their production:
1. Technological Investment
Advanced machinery and technologies such as CNC machines and EDM can be expensive. Small manufacturers may find it challenging to invest in state-of-the-art equipment, which may impede their ability to produce high-quality molds.
2. Skilled Labor Shortage
The production of precision molds requires highly skilled operators who understand the intricacies of the machinery and design. There is a growing shortage of skilled workers in the manufacturing sector, which can impact productivity and quality.
3. Material Selection
Choosing the right material for mold production is critical. Materials must withstand high pressure, temperature, and wear. Failure to select suitable materials can lead to mold failure, which significantly affects production timelines.
How to Optimize Production of Precision Mold Parts
To fully leverage the benefits of precision mold parts, businesses should consider the following optimization strategies:
1. Invest in Technology
Embrace cutting-edge technologies to improve mold design and production processes. Techniques such as 3D printing can be particularly useful for prototyping and refining designs before full-scale production.
2. Continuous Training
Keep your workforce skilled and knowledgeable. Investing in training programs ensures employees are up-to-date with the latest manufacturing processes and technologies.
3. Focus on Quality Control
Implement strict quality control measures throughout the production process. Regularly inspecting molds and the final products will help identify issues early, reducing waste and enhancing quality.
The Future of Precision Mold Parts
The future of precision mold parts looks promising, with several trends shaping the landscape:
1. Automation and Robotics
The integration of automation and robotics in manufacturing is on the rise. These innovations promise higher precision, reduced labor costs, and increased productivity.
2. Sustainable Practices
As companies strive for eco-friendliness, the use of sustainable materials and manufacturing practices in mold production will become increasingly important. This shift can attract environmentally conscious consumers and clients.
3. Advanced Materials
Researchers are exploring new materials that offer enhanced performance characteristics for precision molds. Innovations in polymers and composites are expected to play a significant role in the future of mold manufacturing.
Conclusion
*Precision mold parts* are undeniably crucial in the manufacturing sector, influencing quality, efficiency, and overall production costs. Understanding their significance and the latest trends in the industry equips businesses to make smarter, more informed decisions. As manufacturers continue to innovate and invest in technologies and skilled labor, the future of precision engineering looks brighter than ever.
For metal fabricators looking to enhance their processes, the integration of precision mold parts is no longer an option but a necessity. Explore how adopting these components can revolutionize your production and help you stay competitive in a demanding market.