The Integral Role of Surgical Instruments Manufacturers in Healthcare
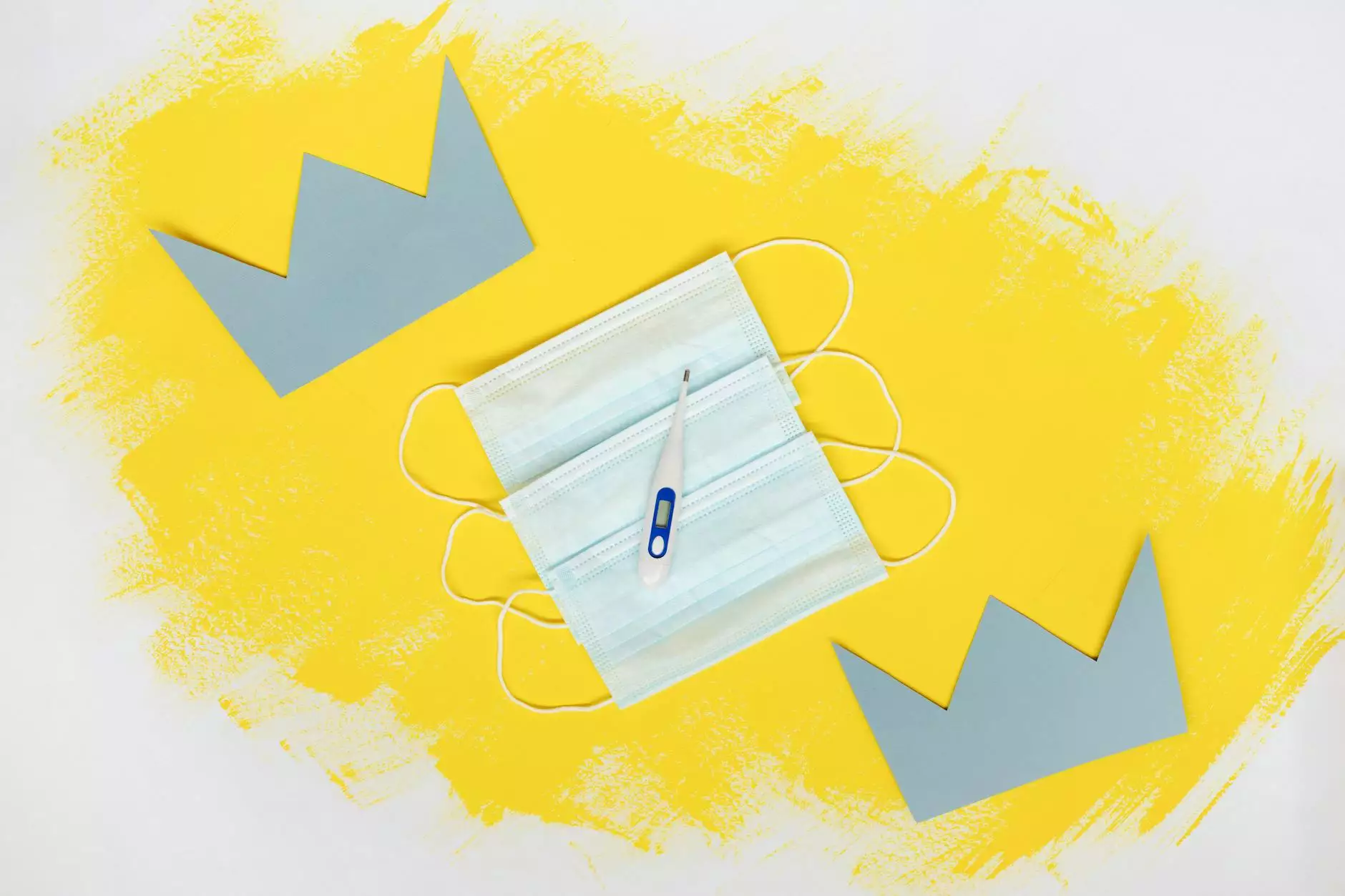
In the modern landscape of healthcare, the importance of surgical instruments manufacturers cannot be overstated. They are the backbone of surgical procedures, providing the essential tools that surgeons and medical professionals rely on daily. This article delves deeply into the world of surgical instruments, exploring the various types, manufacturing processes, emerging technologies, and the pivotal role these manufacturers play in enhancing patient outcomes.
1. An Overview of Surgical Instruments
Surgical instruments are specialized tools designed for performing specific actions during surgical procedures. They range from cutting and dissecting instruments to clamping, suturing, and retracting devices. The wide array of surgical instruments available reflects the complexity and variety of surgical procedures, ensuring that medical professionals have the right tools at their disposal.
1.1 Types of Surgical Instruments
- Cutting Instruments: These include scalpels, scissors, and razors used for making incisions or excisions.
- Grasping Instruments: Tools like forceps and clamps that help hold tissues together during an operation.
- Hemostatic Instruments: These are used to control bleeding. Examples include hemostats and artery clamps.
- Suction Instruments: Devices designed to remove fluids from the surgical site, ensuring visibility and accessibility.
- Suturing Instruments: Tools such as needle holders and suture scissors that facilitate the closing of wounds.
2. The Manufacturing Process of Surgical Instruments
The manufacturing of surgical instruments is a meticulous process that requires precision engineering and an unwavering commitment to quality. Manufacturers must adhere to stringent regulations and standards during every phase of production.
2.1 Material Selection
Quality surgical instruments are typically made from high-grade materials, such as stainless steel, titanium, and various alloys. These materials are chosen for their durability, resistance to corrosion, and ability to maintain sharpness. The selection of the right material is crucial in ensuring the instrument’s efficacy and longevity.
2.2 Design and Prototyping
Before mass production, detailed designs and prototypes are created. This phase involves collaboration between engineers, designers, and medical professionals to ensure that the instruments meet the needs of the surgical teams while also adhering to safety standards.
2.3 Precision Manufacturing Techniques
Surgical instrument manufacturing involves several advanced techniques, including:
- CNC Machining: Computer Numerical Control (CNC) machining allows for precise cutting and shaping of instruments.
- Electro-polishing: This process enhances the surface finish and reduces the risk of contamination.
- Thermal Treatments: These processes improve the hardness and elasticity of the instrument materials.
3. The Role of Quality Control in Surgical Instrument Manufacturing
Quality control is a critical aspect of the surgical instrument manufacturing process. Manufacturers implement rigorous testing to ensure that all products meet the necessary safety and performance standards.
3.1 Regulatory Compliance
Manufacturers must comply with regulations set by authorities such as the FDA in the United States or the European Medicines Agency in Europe. This includes rigorous testing and certification processes, ensuring that products are safe for use in medical settings.
3.2 Continuous Improvement Processes
Leading manufacturers employ continuous improvement strategies, such as Six Sigma and Lean Manufacturing, to minimize waste, reduce defects, and enhance overall product quality. This commitment to improvement helps manufacturers to innovate and stay ahead in a competitive market.
4. The Impact of Technology on Surgical Instruments Manufacturing
The advent of new technologies has revolutionized the manufacturing of surgical instruments. Integrating cutting-edge technology enables manufacturers to create more sophisticated and effective tools.
4.1 3D Printing in Surgical Instruments
3D printing technology has emerged as a groundbreaking method in manufacturing surgical instruments. This allows for:
- Customization: Instruments can be tailored to the specific needs of individual patients or surgeries.
- Cost Efficiency: Reduced material waste and lower production costs.
- Rapid Prototyping: Manufacturers can quickly create prototypes for testing and feedback.
4.2 Robotics and Automation
Automation in production lines enhances the efficiency and consistency of manufactured instruments. Robotic systems can perform repetitive tasks with high precision, ensuring that each instrument meets the exact specifications.
5. Challenges Faced by Surgical Instruments Manufacturers
Despite the advancements and opportunities within the sector, surgical instruments manufacturers face several challenges that can impact their operations and market positioning.
5.1 Regulatory Hurdles
The stringent regulatory environment can slow down the introduction of new products to the market. Compliance with safety and efficacy regulations requires significant investments in testing and documentation.
5.2 Supply Chain Disruptions
Global events, such as pandemics or geopolitical tensions, can disrupt the supply chain for essential materials. Manufacturers must cultivate resilience against such disruptions by diversifying their supply sources and maintaining robust inventory levels.
6. Market Trends in Surgical Instruments Manufacturing
Staying abreast of market trends is vital for manufacturers to remain competitive. Some emerging trends include:
6.1 Minimally Invasive Surgery (MIS)
With the growing demand for minimally invasive procedures, manufacturers are focusing on developing instruments that facilitate these surgeries. These tools are designed to reduce patient recovery times, minimize scarring, and enhance surgical precision.
6.2 Digital Integration
The integration of digital technologies, such as augmented reality and AI, is also beginning to influence surgical practices. Manufacturers are exploring how to incorporate these technologies into their instrument designs to improve surgical outcomes and training.
7. Selecting the Right Surgical Instruments Manufacturers
For healthcare providers, choosing a reliable surgical instruments manufacturer is critical to ensuring operational success and patient safety.
7.1 Factors to Consider
- Quality and Compliance: Verify the manufacturer’s adherence to industry standards and certifications.
- Reputation and Experience: Assess the manufacturer’s track record in the industry.
- Customer Support: Evaluate the level of support provided post-purchase, including training and maintenance.
7.2 Building Long-term Partnerships
Establishing a strong partnership with surgical instrument manufacturers can yield numerous benefits, including better pricing, priority shipping, and collaboration on future advancements.
8. Conclusion
The role of surgical instruments manufacturers in healthcare is fundamental. They ensure that medical professionals have access to the highest quality tools necessary for surgery, impacting patient outcomes and the overall efficiency of healthcare systems. As technology advances and new challenges arise, these manufacturers must continue to innovate while maintaining rigorous standards of quality and compliance. By leveraging the latest advancements and fostering strong partnerships with healthcare providers, surgical instruments manufacturers can further solidify their position as vital contributors to the medical field.
For those looking to explore top-tier surgical instruments, New Med Instruments at new-medinstruments.com represents a commitment to excellence in the health and medical sectors, offering a range of high-quality medical supplies that meet the needs of today's dynamic healthcare environment.